Electron Issue 114
Keeping you up to date with the latest regulatory changes, exam reports, technical issues, consultation results and other issues affecting electrical workers - published June 2022.
Presiding Member's update
The year is half over, and electrical workers continue to be challenged by changing work environments and economic factors. At times, work and financial pressures can seem to be overwhelming.
It is encouraging, however, that workers are becoming more comfortable talking about issues and that more resources to help are becoming available. If you need to reach out, you can contact the likes of Mates in Construction or call 1737, a freephone line where you can talk to a trained counsellor.
In this issue of the Electron, there are a number of safety articles, and one that discusses minimum standards. The Board often hears cases where a practitioner has cut corners to keep costs down or to appease clients. Doing so can put persons and property at risk and expose the electrical worker to civil liability and to disciplinary action before the Board. Put simply, the envisaged savings are just not worth it.
You will also see a request from the Registrar to check your details on the new licensing platform. Accurate data about electrical workers ensures important communications arrive in a timely manner.
Mel Orange
Presiding Member
Registrar update
Kia ora koutou,
Welcome to the June 2022 edition of Electron.
It’s hard to believe how quickly this year is going. I am already heartened by several optimistic indicators that look promising for the future prosperity of our industry.
One of the positive signs for me has been changes to the vocational education system and initiatives to increase the number of people undertaking trade training. In particular, the Apprenticeship Boost which has been introduced as part of the wider Government Apprenticeship Support Programme — a cross-agency response to help employers support their employees in formal training, including apprenticeships. More about apprentice boost and what this may mean for your apprentices, business or eligibility is available from this link:
Apprenticeship Boost(external link) — Tertiary Education Commission
You may also be interested to learn more about vocational education changes and the role of Waihanga Ara Rau (Construction & Infrastructure) Workforce Development Council in the development of electrical industry qualifications and training standards.
Waihanga Ara Rau (Construction & Infrastructure) Workforce Development Council(external link)
As you should all be aware, the new electrical workers licensing platform is up and running. I would urge all practitioners to check the public register to ensure their displayed information is complete and accurate. The platform has the flexibility for persons to update a certain amount of this public information from their individual portal. Guidance on what can be changed and how to do this is available from the following link:
Guide to the EWRB Practitioner Portal for Licensing - Overview
If you are having difficulties, or there is information that you think is still not correct, then please let the licensing team know as soon as possible:
Fit and Proper Person declarations
The Board would like to remind all electrical workers about the importance of accurately declaring their “Fit and Proper Person” (F&PP) status when they are submitting a registration or licensing application. If you are unsure or have any reasonable doubts as to whether you meet the F&PP criteria, please contact the Licencing team in the first instance to discuss the matter before making a declaration on your application.
The current F&PP policy is available from the following link:
Fit and Proper Persons [PDF, 524 KB]
I would like to introduce and highlight some of the featured articles in this edition of the Electron.
Featured standard
NZS 4219:2009 Seismic performance of engineering systems in buildings is cited to comply with the seismic requirements of several Building Code clauses. It also has particular importance regarding the application to electrical supply and distribution fittings within multi-storey apartments and commercial buildings. I would recommend all those persons designing or installing electrical installations in these areas become familiar with the appropriate requirements of this Standard.
Important message - safe living with electricity
This article graphically demonstrates dangerous life threating incidents that can result from the use of everyday domestic appliances and the dangers of overloading Electrical Portable Outlet Devices (EPODs) commonly known as power boards, or multi-boxes. It contains images supplied by WorkSafe of appliances and fittings that have caused electrical fires and provides advice on good practice to mitigate these events.
Finally, take care, work safely, and thank you for taking the time to read the Electron.
If you have any comments or suggestions for future Electron editions, please let me know by emailing registrations@ewrb.govt.nz.
Noho ora mai,
Duncan Connor
Registrar of Electrical Workers
Standard of the Month
Featured standard
NZS 4219:2009 Seismic performance of engineering systems in buildings
Featured Standard NZS 4219:2009 Seismic performance of engineering systems in buildings sets out the criteria for the seismic performance of engineering systems related to a building’s function. It is intended to prevent the loss of life and provide protection by ensuring all systems are securely restrained and those with emergency lifesaving functions continue to operate during and following an earthquake.
This Standard will be particularly useful for sub-trade work in multi-storey apartments and commercial buildings. It covers the design, construction, and installation of seismic restraints for engineering systems such as air-handling units, cabinets, pipework and ductwork, and all electrical supply and distribution fittings. This includes, but is not limited to, switchboards; cable trays; conduit sleeved penetrations allowing movement for cables entering buildings through foundations; fixings for recessed and suspended luminaires; resilient mountings for emergency electrical systems; and batteries, as well as communication, data, and control systems.
This is one of the over 90 Standards that are available for all licenced electrical workers to access from EWRB Online Portal.
Important message - safe living with electricity
With colder weather approaching, more prevalent and sustained use of home heating appliances can result in higher electrical loading and increased safety risks.
It would be an opportune time to not only check your own home but to also raise public awareness about the importance of regular testing and checking of electrical appliances, with a focus on recommending vigilance and what warning signs to look out for.
Heaters, toasters, electric blankets, and kettles leads with loose connections or compromised insulation can be deadly and can cause electric shocks or fires.
WorkSafe have advised that they have received a concerning number of fire incident notifications resulting from the misuse (overloading) of EPODs, commonly known as power boards or multi-boxes.
Further useful information and advice for your customers is available from the links below:
Electron issue #103 – Living safely with electrical multi-boxes
Using electric blankets safely(external link) — WorkSafe
How to identify loose connections(external link) — WorkSafe
Notifying WorkSafe of Danger
WorkSafe and Energy Safety reminds electrical workers of the importance of notifying both the owner and WorkSafe of any immediate danger they identify when carrying out prescribed electrical work (PEW). Even if the danger has been removed, the reporting provides valuable information on the safety of electrical installations and equipment which enables WorkSafe to identify and respond to trends and broader safety issues.
It is important to notify the owner and WorkSafe as soon as practicable, especially if the danger has not been removed, to enable the owner and WorkSafe to take remedial action. Please note, Regulation 19 applies to immediate danger to life or property identified while carrying out any PEW, periodic assessment, or when examining a connectable installation with the view of issuing a Warrant of Electrical Fitness (WoEF).
The notification should be as full as possible and include details of the nature of the danger, any equipment involved, how and why it is an immediate danger, and what steps have been (or should be) taken to minimize or eliminate the danger. Regulation 19 of the Electricity (Safety) Regulations 2010 outlines this requirement and can be located on the New Zealand Legislation website.
Regulation 19 – Notifying Worksafe of danger(external link) — New Zealand Legislation
Periodic Assessments of Hazardous Area Electrical Installations
Recent WorkSafe/Energy Safety audits of periodic assessments for hazardous area electrical installations have found that the documentation supplied to the owner or operator was not in line with the requirements of the applicable Standard(s).
AS/NZS 60079.17, cited by regulation 75(1)I, outlines the requirements for documentation to be completed during the assessment, this includes the completion of checklists outlined in the different tables depending on the protection technique being used. This could lead to the owner or operator, as well as the person carrying out the periodic assessment (being PCBUs, i.e. a person conducting a business or undertaking), being held accountable for non-compliance of the hazardous area installation.
The documentation supplied to the owner or operator must include the details of the type of inspection being undertaken on the equipment and full details of the assessment findings in the relevant format, as specified in AS/NZS 60079.17.
Regulations and Standards are the Minimum
Complaints resulting in disciplinary hearings that come before the Board are often due to negligent, incompetent, non-compliant, or unsafe electrical work.
In accordance with WorkSafe/Energy Safety “Good Practice Guidelines”, the Electricity (Safety) Regulations 2010, in defining ‘safe’ and ‘unsafe’, expresses the principle that there is a zone between what is defined as being safe and what is defined as being unsafe. This zone recognises safe practices, and practices that are deemed to be unsafe, within an optimal upper safety limit and a lower tolerance limit.
WorkSafe/Energy Safety Good Practice Guidelines [PDF 2.39 MB](external link) — WorkSafe
Using recognized and appropriate standards for installation practices is one way to ensure the minimum required level of safety is achieved.
Part 1 of the Electrical Installations Standard, AS/NZS 3000 (“the Wiring Rules”) provides for uniform essential elements that constitute the minimum regulatory requirements for a safe electrical installation. Part 2 provides installation practices that comply with the essential safety outcomes of Part 1.
The Board has identified installations that, in varying degrees, are concerning examples of very poor and substandard work practices, in a number of recent disciplinary matters. These include installations wired to comply with Part 2 of the Wiring Rules that fall well below the minimum line of tolerance by being unsafe and/or non-compliant, while other areas of that same installation reflect a bare minimum level of fitness and less than ideal work practices.
Beyond the scope of individual competence, if a practitioner has only planned to do the work to a bare minimum standard, then there is little margin for error if things go wrong.
External factors outside the practitioner’s control, such as time pressures or commercial costs, can result in shortcuts with unintended and detrimental effects on the final safety and compliance outcomes of an installation.
One way to mitigate this is to plan to do the work to a standard above the minimum and to aim for a higher optimal safety level.
Nothing in the legislation restricts a practitioner from working above and beyond the minimum standard. In fact, it may often be true that it can be in the clients’ and practitioners’ best interests to recommend and to work to a higher standard to future-proof and increase the quality and fitness of the installation, which in turn can also lead to greater client satisfaction and positive reviews.
The difference between an excellent job and a barely adequate or non-compliant job can sometimes come down to planning, communication, taking pride in one’s work, and applying the best “on job” work practices.
Careers – Technical Officer (WorkSafe, Wellington)
WorkSafe’s Energy Safety team are looking for a Technical Officer (Electrical). In this regulatory role, you’ll liaise with the best in New Zealand industry, and have a significant impact on electricity safety through interventions which change industry and public behaviour. Ideally you will have qualifications in an Electrical trade or related occupation, sound industry experience and technical knowledge, plus a good understanding of electricity industry issues and the wider stakeholder network. This is a permanent role based in Wellington (but open to other locations for the right person).
For more information please use the following link:
Technical Officer (Electrical), Wellington(external link) — WorkSafe Careers
Interview with Monica Kershaw (Board Member)
Monica Kershaw is an experienced Industrial Electrician and Industrial Measurement and Control Technician, as well as a Senior Lecturer and Technology Lead for Specialist Trades at the Manukau Institute of Technology. Outside of her career titles, she is also a mum and wāhine of proud Fijian descent. After refining her skills in the field for the first part of her career, she decided to move into teaching when she was starting her family for a more balanced work-life split. She shares some of her insights and learnings in this Q&A.
What encouraged you to join the electrical industry?
My journey with the electrical industry started right back when I was a pre-schooler. From as far back as I can remember, I’ve felt this need to know how things were put together, to know how everything worked. Mum likes to recall a particular incident where she came in to find me with a screwdriver, ready to take a power-point apart. So, I think it was definitely that curiosity which was the main driver for me becoming passionate about the industry.
Were you able to start your training toward a trade in high school?
Even though I knew I wanted to train in the electrical industry from such a young age, this was put on hold for a few years while I attended a Catholic Girls School. At the time, young women like me weren’t exactly enthusiastically encouraged to pursue tech at school. So, this time was spent in sewing and typing classes instead. After I left school however, I went straight into polytechnic to work toward becoming an Industrial Electrician.
What has continued to motivate you in your mahi?
Curiosity and a desire to figure out the unknown pulled me into the industry. But what has kept me here is how I’ve been able to practice my cultural needs and weave it into my mahi, especially over the past decade that I’ve been teaching. In Pacific cultures, history and knowledge is passed down through generations by oral traditions, song, and dance. Being able to use those skills to weave the oral traditions that I grew up with when it comes to my teaching has been so enriching. I teach at Manukau Institute of Technology, which has the largest number of Māori and Pasifika students out of any institution in Aotearoa, so being able to bring my culture to work and to share those traditions with my students is important. It builds connection and belonging for them, and for myself and other Lecturers.
For young wāhine entering the trade, I think it’s about them being able to see role-models who they can connect with, as well as with young Māori and Pasifika coming to get their qualifications. The opportunity to be one of those gateways and supports has been my biggest motivation.
If you had to pinpoint one career highlight so far, project, or moment, what would that be?
I think ‘on paper’, the answer would be when I was named the Top Overall Apprentice of the Year at BHP New Zealand Steel where I completed my apprenticeship. But I think personally it’s what I’ve touched on already – watching that next generation come up and take their place in the industry. Being on that journey with students, feeling that pride and excitement with them when they get their registration, it’s just so awesome each time. It never gets old.
So, for me that’s been the highlight of my career, celebrating my student’s successes with them, and feeling like my work whānau is forever growing.
As a Board Member, what changes would you like to see for the industry to become more diverse and inclusive for wāhine and other groups such as Māori and Pasifika?
I think it’s about increasing the support and resources for employers also. There are a lot of Women in Trades events directed at young wāhine, but there are no events directed at employers. Currently a lot of the work being done is encouraging high-school leavers to enter trades, and convincing them why it’s a great pathway, which of course is essential too. But what I’d like to see more of is outreach and engagement with potential employers who will be hiring these young people, so we can continue to build healthy and supportive working environments for apprentices to step into.
Right now, the advice and information available for how employers can create diverse and inclusive spaces in their workplaces is lacking. There are opportunities here for industry groups and regulators to provide spaces for educating these parts of the industry. Increasing the opportunities for employers to learn and seek guidance could be transformative. Tapping into resources such as myself and other women in industry and running mentoring sessions and Q&A’s is something that should really be looked at.
What do you think might be stopping young wāhine from joining the industry currently?
This is a tricky one. Kylie from Women in Trades has been doing some awesome work developing resources to understand this better and through this work some barriers have been identified, but there are still gaps.
Again, I think it also requires changing industry perspectives higher up. So, focusing on supporting employers to better understand how to manage and encourage women in their businesses. I think there are cultural aspects to overcome too, such as us collectively getting better at encouraging young women early in schooling and normalising trades as attractive career pathways.
Are there any final pieces of advice you’d like to share with others in the industry on how to create safe and empowering environment for women in the industry?
Communication is key, and if you’re wondering how to best support or encourage someone to be their best self at work, ask! Don’t be afraid to ask people when you aren’t sure and lean into the not knowing. I think a lot of the time it’s just that people don’t want to feel out of their depth but being okay with feeling uncomfortable is crucial for building your understanding and cultural capabilities.
The more we encourage people to ask for help when there’s something they’re unsure about, the better. This means increasing access to channels and groups for employers to feel connected to different perspectives and knowledge throughout the industry also.
The last bit of advice I have is to practitioners: please encourage the wāhine around you at mahi, like you would your sister, daughter, granddaughter, cousin, or niece. Also, to the men who have women in their whānau who want to join the electrical industry or other trades, encourage them, and help them on their way.
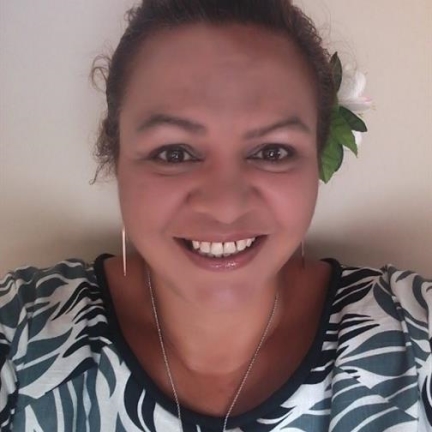
Image courtesy of Monica Kershaw.
Disciplinary hearings
The Board dealt with one electrical worker in April 2022 in relation to two separate complaints made about him. The electrical worker accepted responsibility for his wrongdoing on both matters.